A continuación os mostraré mi pequeña contribución al mundo de la ciencia y más concretamente de la Ingeniería Química.
Y os preguntaréis (no creo, pero bueno, queda bonito al inicio de la frase), porque sobre este tema y no sobre la cría de los moluscos en cautividad. La razón es sencilla, es lo que he dedicado mis estudios universitarios, los cuales los he realizado en la "fabulosa y espectacular" (las comillas las he colocado expresamente) ETSEQ de la URV
Tonterías a parte, espero que os pueda servir de algo esta sección.
Equivalencias de presión
Equivalencias de calor, energía y trabajo
Composición del aire limpio y seco cerca del nivel del mar
Constante de los gases ideales
Factores de conversión
Válvulas de seguridad
Termodinámica básica
Secado de la madera
Operaciones de separación
Bioseparación, cromatografía de gel
Obtención del cloruro de vinilo
Plásticos
Hidrogenación catalítica selectiva de CFC’s
Proceso de obtención del Permanganato potásico
Equivalencias de presión
Factores de conversión entre las diferentes formas de medir la presión.
mm Hg | in Hg | bar | atm | kPa |
---|---|---|---|---|
1 | 3.937 e-2 | 1.333 e-3 | 1.316 e-3 | 0.1333 |
25.40 | 1 | 33.87 | 3.342 e-2 | 3.387 |
750.06 | 29.53 | 1 | 0.9869 | 100.0 |
760.0 | 29.92 | 1.013 | 1 | 101.3 |
75.02 | 0.2954 | 0.01 | 9.872 e-3 | 1 |
Equivalencias de calor, energía y trabajo
Factores de conversión entre las diferentes formas de medir el calor, energía y el trabajo.
ft lbf | kWh | hp hr | Btu | caloria | Joule |
---|---|---|---|---|---|
0.7376 | 2.773 e-7 | 3.725 e-7 | 9.484 e-4 | 0.2390 | 1 |
7.233 | 2.724 e-6 | 3.653 e-6 | 9.296 e-3 | 2.3438 | 9.80665 |
1 | 3.766 e-7 | 5.0505 e-7 | 1.285 e-3 | 0.3241 | 1.356 |
2.655 e6 | 1 | 1.341 | 3.4128 e3 | 8.6057 e5 | 3.6 e6 |
1.98 e6 | 0.7455 | 1 | 2.545 e3 | 6.4162 e5 | 2.6845 e6 |
74.73 | 2.815 e-5 | 3.774 e-5 | 9.604 e-2 | 24.218 | 1.0133 e2 |
3.086 e3 | 1.162 e-3 | 1.558 e-3 | 3.9657 | 1000 | 4.184 e3 |
7.7816 e2 | 2.930 e-4 | 3.930 e-4 | 1 | 2.52 e2 | 1.055 e3 |
3.086 | 1.162 e-6 | 1.558 e-6 | 3.97 e-3 | 1 | 4.184 |
Composición del aire limpio y seco cerca del nivel del mar
Composición del aire limpio y seco cerca del nivel del mar.
Componente | % volumen = % mol |
---|---|
Nitrógeno | 78.084 |
Oxígeno | 20.9476 |
Argón | 0.934 |
Dióxido de carbono | 0.0314 |
Neón | 0.001818 |
Helio | 0.000524 |
Metano | 0.0002 |
Kriptón | 0.000114 |
Oxido nitroso | 0.00005 |
Xenón | 0.0000087 |
Ozono | |
|
0-0.000007 |
|
0-0.000002 |
Amoníaco | 0-trazas |
Monóxido de carbono | 0-trazas |
Yodo | 0-000001 |
Dióxido de nitrógeno | 0-000002 |
Dióxido de azufre | 0-0.0001 |
Constante de los gases ideales
Factores de conversión del valor de la constante de los gases ideales ( R ).
1.987 cal / (g mol) K = Btu / (lb mol) ºR
10.73 psia ft3 / (lb mol) ºR
8.314 kPa m3 / (kg mol) K = 8.314 J / (g mol) K
82.06 cm3 atm / (g mol) K
0.08206 l atm / (g mol) K
21.9 inHg ft3 / (lb mol) ºR
0.7302 ft3 atm / (lb mol) ºR
Factores de conversión
Factores de conversión entre diferentes medidas entre el Sistema Internacional y el Sistema Inglés,
Area | 1 ft2 = 0.0929 m2 |
1 in2 = 6.452 x 10-4 m2 | |
Capacidad térmica | 1 Btu/(lb)(°F) = 4187 J/kg K |
Coeficiente de transferencia térmica | 1 Btu/(hr)(ft2)(°F) = 5.678 W/m2 K |
Densidad | 1 lb/ft3 = 16.018 kg/m3 |
1 slug/ft3 = 515.379 kg/m3 | |
Conductividad térmica | 1 Btu/(hr)(ft)(°F) = 1.731 W/m. K |
Difusividad térmica | 1 ft2/sec = 0.0929 m2/s |
1 ft2/hr = 2.581 x 10-5 m2/s | |
Energia | 1 Btu = 1055.1 J |
1 cal = 4.186 J | |
1 (ft) (Ibr) = 1.3558 J | |
1 (hp)(hr) = 2.685 x 106 J | |
Energía especifica | 1 Btu/lbm = 2326.1 J/kg |
Flujo másico por unidad de tiempo | 1 lb/hr = 0.000126 kg/s |
Flujo térmico | 1 Btu/(hr)(ft2) = 3.1525 W/m2 |
Flujo térmico por unidad de tiempo | 1 Btu/hr= 0.2931 W |
1 Btu/s = 10055.1 W | |
Flujo térmico por unidad de volumen | 1 Btul(hr)(ft3) = 10.343 W/m3 |
Fuerza | 1 lbf = 4.448 N |
Longitud | 1 fl = 0.3048 m |
1 in = 2.54 cm = 0.0254 m | |
1 mile = 1.6093 km = 1609.3 m | |
Masa | 1 lb = 0.4536 kg |
1 slug = 14.594 kg | |
1 lbm/ s = 0.4536 kg/s | |
Potencia | 1 hp = 745.7 W |
1 (ft)(lb)/s = 1.3558 W | |
1 CV = 735.4 W | |
1 Btu/s = 1055.1 W | |
1 Btu/hr = 0.293 W | |
Presión | 1 lb/in2 = 6894.8 N/m2 |
1 lb/ft2 = 47.88 N/m2 | |
1 atm = 101.325 N/m2 | |
Resistencia térmica | 1 (hr)(°F)/Btu = 1.8958 K/W |
Temperatura | T(°R) = (9/5)T(K) |
T(° F) = [T(°C)] (9/5) + 32 | |
T(°F) = [T(K) – 273.15](9/5) + 32 | |
Velocidad | 1 ft/s = 0.3048 m/s |
1 mph = 0.44703 m/s | |
Viscosidad cinemática | 1 ft2/s = 0.0929 m2/s |
1 ft2/hr = 2.581 x 10-5 m2/s | |
Viscosidad dinámica | 1 lb/(ft)(s) = 1.488 N s/m2 |
1 centipoise = 0.00100 N · s/m2 | |
Volumen | 1 ft3 = 0.02832 m3 |
1 in3 = 1.6387 x 10-5 m3 | |
1 gal (U.S. Iiq.) = 0.003785 m3 |
Válvulas de seguridad
El código de ASME proporciona los requisitos básicos para la protección de sobrepresión. Sección I, acción en las calderas. El resto de los recipientes incluyendo los intercambiadores y los equipos de presión caen bajo la sección VIII. El API RP 520 y algunos otros documentos del API suplen el código ASME en algunos casos. Estos códigos especifican la acumulación permisible, que es la diferencia entre relevar la presión en la cual la válvula alcanza el flujo y la presión por completo en que la válvula comienza a abrirse. La acumulación se expresa como porcentaje de la presión del conjunto en la tabla 1.
Los envases líquidos llenos requieren la protección contra la expansión termal. Tales válvulas de descarga son generalmente absolutamente pequeñas. Dos ejemplos son
1. Agua que se refresca que se puede bloquear adentro con el líquido caliente todavía que fluye en la otra cara de un cambiador.
2. Líneas largas a las granjas de tanque que pueden estar expuestas al sol.
Tabla 1. Acumulación expresada como porcentaje de la presión del conjunto
| Calderas Sección I de ASME | Recipientes de presión Sección VIII de ASME | Diseño típico para los compresores, las bombas y tuberías Líquidas |
LÍQUIDOS | |||
– | 10 | 25 | |
– | 20 | 20 | |
VAPOR AGUA | |||
3 | 10 | 10 | |
– | 20 | 20 | |
GAS O VAPOR | |||
– | 10 | 10 | |
– | 20 | 20 | |
Dimensionado
Utilice las cartas y los datos de los tamaños del fabricante cuando sea disponible. En casos de no disponer de datos de fabricante utilizar la siguiente fórmula:
u = 0.4·sqrt(2 g DP)
donde
DP = pérdida presión en pies de líquido que fluye
u = velocidad en ft/sec
g = 32,2 ft/sec2
Esto dará un área conservadora de la válvula de descarga. Para los líquidos compresibles utilice el DP que corresponde a 1/2 P1 si la diferencia de presión es mayor que la que corresponde a 1/2 P1 (donde ocurre la velocidad acústica). Si la diferencia de presión está por debajo de ésa, utilizar la DP real.
Para los recipientes llenados solamente del gas o del vapor y expuestos al uso del fuego utilizar
A = 0.042 As / sqrt(Pl)
(API RP 520, Referencia 3)
Tabla 2. Tamaños estándares del orificio para las válvulas de descarga de seguridad de acero
Designación Orificio | Área efectiva in2 | Designación Orificio | Área efectiva in2 |
D | 0.110 | L | 2.853 |
E | 0.196 | M | 3.60 |
F | 0.307 | N | 4.34 |
G | 0.503 | P | 6.38 |
H | 0.785 | Q | 11.05 |
J | 1.287 | R | 16.0 |
K | 1.838 | T | 26.0 |
A = área calculada del inyector, in2
P1 = set de presión (psig) x (1 + acumulación de la fracción) + la presión atmosférica, psia.
Por ejemplo si la acumulación = 10%, entonces (1 + acumulación de la fracción) = 1,10
As = superficie del recipiente expuesta, ft2
Está también da resultados conservadores.
La presión del conjunto de una válvula convencional es afectada por la presión posterior. La configuración del resorte se puede ajustar para compensar la presión posterior constante.
Determinación de índices de la descarga
Las causas más comunes de la sobrepresión son
1. Fuego externo
2. Incidente en un Tubo Del Cambiador De Calor
3. Expansión Líquida
4. Incidente en el Agua que enfría
5. Incidente De la Electricidad
6. Salida Bloqueada
7. Fallo de los controles automáticos
8. Pérdida de reflujo
9. Reacción química (este calor puede exceder a veces el calor de un fuego externo)
Las primeras tres causas de la sobrepresión en nuestra lista son más favorables a la generalización que las otras y por tanto serán discutidas.
Fuego
La entrada de información del calor del fuego se discute en API RP 520 (referencia 3). Una forma de la ecuación para el líquido que contiene los recipientes es
Q = 21000 F A0.82
donde
Q = Absorción de calor, Btu/hr
Aw = superficie mojada total, ft2
F = Factor del ambiente
Los factores ambientales representados por F son
Recipiente descubierto = 1.0
Aislado = 0.3/espesror de aislamiento, in.
Almacenaje subterráneo = 0.0
Tierra cubierta sobre el suelo = 0.03
La altura para calcular la superficie mojada debe ser
1. Para el recipientes verticales – al menos 25 pies sobre el suelo o el otro nivel en los cuales un fuego podría ser sostenido.
2. Para los recipientes horizontales – al menos igual al diámetro máximo.
3. Para las esferas – no debe ser mayor o igual a 25 pies.
Incidente en el Tubo Del Cambiador De Calor
1. Utilice el líquido que entra dos veces de la sección transversal de un tubo según lo indicado en API RP 520 (referencia 3).
2. Utilice DP = u2/2 g para calcular salida. Puesto que esto actúa similar a un orificio, necesitamos un coeficiente; utilizar 0.7.
Para los líquidos compresibles, si la pérdida en sentido descendiente es menos que la 1/2 aguas arriba, utilizar ½ de la pérdida aguas arriba como DP. Si no utilice la DP actual.
Expansión Líquida
La ecuación siguiente se puede utilizar para el dimensionado de las válvulas de descarga para la expansión líquida.
Q = BH /500 GC
(Api Rp 520, Referencia 3)
donde
Q = capacidad requerida, gpm
H = entrada de calor, Btu/hr
B = coeficiente de la expansión volumétrica por °F:
= 0,0001 para el agua
= 0,0010 para los hidrocarburos ligeros
= 0,0008 para la gasolina
= 0,0006 para los destilados
= 0,0004 para el fuel-oil residual
G = gravedad específica
C = calor específico, Btu/lb °F
Para un mayor detalle consultar las normativas que se citan en esta pequeña guía.
Termodinámica básica
ENERGIA
1. La energía, que sólo se define entre dos estados de un sistema impermeable, se define como el trabajo adiabático necesario pare pasar de un estado a otro, lo cual permite su medida inequívoca. El trabajo termodinámico es una variable primaria extraída de la Mecánica, pero que en Termodinámica sólo se refiere a la energía mecánica (o equivalente) transvasada a través de una frontera impermeable.
2. El calor es la energía no mecánica (ni equivalente) transvasada a través de una frontera impermeable.
ENTROPIA
1. Las consecuencias del equilibrio son :
– la temperatura de las partes de un sistema en equilibrio ha de ser uniforme.
– no puede haber velocidades relativas entre sus partes.
– los potenciales químicos de las especies conservativas han de ser iguales en todas sus partes (si no hay campos externos de fuerzas).
– la presión de las partes de un sistema en equilibrio ha de ser uniforme (si no hay campos externos de fuerzas).
2. Se define la generación de entropía en un sistema, como el exceso de la variación de entropía del sistema una vez descontada la que fluye por la frontera, y se demuestra que es siempre positiva.
EXERGíA
1. Se demuestra que el trabajo limite (el mínimo necesario o, cambiado de signo, el máximo obtenible) pare pasar de un estado a otro es aquél que no genera entropía en el universo.
2. Se define el trabajo útil como la parte del trabajo total que fluye a través de la frontera y no es intercambiada con la atmósfera (que se considera como trabajo inútil).
3. En cualquier caso, se define la exergía (en realidad sólo su variación entre dos estados) como el trabajo útil mínimo pare pasar de uno a otro, y la irreversibilidad como la diferencia entre el trabajo útil real y el trabajo útil límite.
PRINCIPIOS DE LA TERMODINÁMICA
Los Principios (verdades experimentales que no requieren demostración) en los que se basaba la Termodinámica clásica se pueden resumir así:
Principio Cero: existe una función, que llamamos temperatura, que caracteriza el estado térmico del sistema, tal que si dos sistemas están en equilibrio térmico con un tercero, también lo están entre sí (Maxwell-1870).
Primer Principio: existe una función, llamada energía, que no varia en la evolución que sigue a la liberación de restricciones en un sistema aislado. Si el sistema realiza un proceso cíclico, la energía neta intercambiada en forma de calor y en forma de trabajo son numéricamente iguales (y de signo contrario), lo que indica que se puede definir un equivalente mecánico del calor (Joule- 1842).
Segundo Principio: no se puede extraer indefinidamente (cíclicamente) trabajo a partir de una sola fuente térmica (Carnot-1824) y ello implica que existe una función, que llamamos entropía, que siempre aumenta en la evolución que sigue a la liberación de restricciones en un sistema aislado (Clausius- 1857).
Tercer Principio: la función entropía tiende a cero cuando la temperatura (absoluta) tiende a cero, para toda sustancia en equilibrio termodinámico (Nernst-1906). Este principio sólo se utiliza en la Termodinámica química.
Secado de la madera
Introducción
El secado de productos, entendiendo como tal la deshidratación de los mismos, es una técnica muy antigua utilizada para la conservación de los alimentos. Esta desecación se realizaba con el aprovechamiento con la energía solar y del viento.
Esta técnica se viene aún empleando, si bien la mayoría de los procesos requieren de esta operación básica de un modo más industrial. Lo cierto es que, a pesar de ser una tecnología antigua, no se encuentra altamente desarrollada y hasta hace pocos años estos procesos industriales eran bastante imperfectos y daban como resultado productos mediocres.
Un alto control de las variables que entran a formar parte del proceso de secado: temperatura y humedad relativa del aire, y velocidad de circulación del mismo, son imprescindibles para obtener un producto de calidad y homogéneo. Hoy en día los sistemas de regulación, control y mando, ofrecen la posibilidad de regulaciones muy finas, que permiten poder ofrecer sistemas muy seguros y versátiles.
La bomba de calor se presenta como una de las tecnologías más adecuadas para el secado de productos, gracias a que permite el control no sólo de la temperatura de secado, sino también de la humedad relativa de la cámara, con independencia de las condiciones exteriores.
El secado de la madera
El producto
La madera es un tejido vivo no inerte, cuyo equilibrio está ligado a las funciones vitales del árbol. Por lo tanto, su degradación comienza con la tala del mismo. Desde este momento se hace necesario un nuevo equilibrio con el medio, de manera que se pueda obtener un producto útil y duradero. De este modo, la calidad, duración y propiedades de los productos elaborados con madera, estarán en relación directa al proceso de secado que ha sufrido la misma.
Las dos condiciones que deben cumplirse para el secado de estos productos son:
– conseguir una humedad adecuada, en función de la aplicación prevista.
– Reparto uniforme de la humedad, de madera que no se produzcan fisuras ni tensiones.
El secado en circuito cerrado de aire, con control sobre la temperatura y humedad de la cámara de secado, supone una de las mejoras tecnologías para el secado de la madera. Esto se consigue mediante la aplicación industrial de la Bomba de calor.
El proceso de secado tradicional.
El aire, impulsado por los ventiladores, atraviesa el sistema de calefacción, donde se calienta hasta la temperatura fijada; posteriormente pasa por un sistema de humidificación, que permite que se humedezca si está demasiado seco. Una vez climatizado, el aire se dirige a las pilas, de manera que atraviesa los espacios libres que quedan entre los talones apilados. Conforme el aire atraviesa las pilas, se va cargando de humedad y disminuyendo su temperatura.
Una vez el aire, frío y húmedo se encuentra al otro lado de la carga de madera es absorbido por los ventiladores, para completar el circuito y volver a repetir el proceso anterior. En el circuito de retorno, una parte del aire cargado de humedad al exterior, por trampillas de ventilación, a veces ayudadas por ventiladores de extracción. Al mismo tiempo, se da entrada a aire exterior, más frío y seco que el interior, lo que hace bajar la temperatura y la humedad relativa del interior.
Cabe señalar que aunque el aire exterior tenga una humedad relativa muy alta, normalmente la elevación térmica del sistema hace que baje fuertemente su humedad, por lo que desciende la humedad relativa del secadero.
En ocasiones, para minimizar las pérdidas de calor en un secadero, se sitúa un intercambiador entre el aire de entrada y el de salida.
El secado de la madera por bomba de calor.
La aplicación de la tecnología de Bomba de calor al secado de la madera permite la utilización de un circuito cerrado de aire en el proceso, ya que al aprovecharse la posibilidad de condensación de agua por parte de la bomba de calor, de manera que no es necesaria la entrada de aire exterior para mantener la humedad relativa de la cámara.
El circuito será el siguiente: el aire que ha pasado a través de la madera -frío y cargado de humedad- se hace pasara través de una batería evaporadora -foco frío- por la que pasa el refrigerante (freón R-134a) en estado líquido a baja presión. El aire se enfría hasta que llegue al punto de roció y se condensa el agua que se ha separado de la madera. El calor cedido por el agua al pasar de estado vapor a estado líquido es recogido por el freón, que pasa a vapor a baja a presión. Este freón en estado gaseoso se hace pasar a través de un compresor, de manera que disponemos de freón en estado gaseoso y lata presión, y por lo tanto alta temperatura, que se aprovecha para calentar el mismo aire de secado y cerrar el ciclo. De esta manera disponemos de aire caliente y seco, que se vuelve a hacer pasar a través de la madera.
La gran importancia de este ciclo se debe a que al no hacer que entren grandes cantidades de aire exterior, no se rompa el equilibrio logrado por la madera, y no se producen tensiones, de manera que se logra un secado de alta calidad.
Las etapas del secado de la madera.
El secado de la madera se realiza en cámaras cerradas, por lotes, haciendo pasar la cámara por diferentes etapas:
– Etapa de precalentamiento: Tiene una duración aproximada de 20 h. En esta etapa se calienta la madera. En nuestro caso, se emplea un circuito de agua caliente, obtenido a partir de sistemas tradicionales. Este proceso inicial de calentamiento lento mejora la calidad del secado final y el inicio del funcionamiento de la bomba de calor, ya que no se conecta hasta que la temperatura de la cámara haya alcanzado una temperatura prefijada, con un nivel de humedad adecuado.
– Etapa de deshumidificación: Entra en actuación la bomba de calor, para eliminar el agua procedente de la madera, con temperaturas entre 55-65ºC: Para cada tipo y grosor de la madera se establecen una curvas de secado, de manera que se van avanzando etapas, cada vez con mayor temperatura y menor humedad relativa en el ambiente, conforme se va avanzando en el secado de la madera. De este modo, la madera no sufre gradientes excesivamente altos. La circulación del aire es invertida cada 12 h, de manera que se obtenga la mayor uniformidad posible.
– Etapa de estabilización: El enfriamiento de la cámara se produce de manera controlada, para que la madera no sufra choques bruscos que puedan provocar torceduras en las fibras o fisuras.
Hasta aquí el resumen del trabajo que hice en la universidad sobre el secado de la madera, pero hoy os traigo el original de dicho documento, más extenso y que curiosamente realice en inglés, ya que los cursos de doctorado eran en esa lengua. Por si lo estáis pensando, no, no me fui a estudiar al extranjero, es que en Tarragona somos así de chulos, en vez de que los estudiantes aprendan el idioma de aquí, las clases se hacen en inglés para así captar estudiantes de todo el mundo. Llevo toda la tarde pensando, como pude hacer un trabajo en ese idioma, no lo recuerdo, porque mi nivel de inglés es bastante limitado. Supongo que acabe tirando de copiar y pegar del texto de la bibliografía.
Operaciones de separación
Las operaciones de separación más importantes de la industria química son las siguientes:
COLUMNA DE DESTILACIÓN
ABSORCIÓN GAS-LÍQUIDO
EXTRACCIÓN LÍQUIDO-LÍQUIDO
INTERCAMBIO IÓNICO
SEPARACIÓN POR MEMBRANA
ÓSMOSIS INVERSA
CENTRIFUGACIÓN
SEPARACIÓN ELECTROSTÁTICA
COLUMNA DE DESTILACIÓN
Principios de operación
Este es uno de los tipos de dispositivos de transferencia de materia más utilizados en la industria, consistente en el acoplamiento de unidades o etapas sucesivas. Una unidad o etapa recibe dos corrientes, una fase V y una fase L, procedentes de dos etapas adyacentes, se ponen en contacto y se descargan las fases L y V, respectivamente, hacia las mismas unidades adyacentes. Para que exista transferencia de materia es preciso que las corrientes que entran en cada etapa no estén en equilibrio, ya que es la separación de las condiciones de equilibrio lo que proporciona el gradiente para la transferencia. Las corrientes que salen no están generalmente en equilibrio, pero sí mucho más próximas al mismo de lo que lo estaban las corrientes de entrada. La proximidad al equilibrio depende de la eficacia de la mezcla y de la transferencia de materia entre fases. Para simplificar el diseño se supone que las corrientes que salen de las etapas están en equilibrio, concepto de etapa ideal, y con posterioridad se aplica un factor de corrección o eficacia para tener en cuenta esta separación del equilibrio.
Descripción de la instalación
Se alimenta a la columna cerca de su parte central con un determinado flujo y una concentración definida. El plato en el que se introduce la alimentación recibe el nombre de plato de alimentación. Todos los platos por encima de éste, constituyen la sección de rectificación, mientras que todos los platos por debajo de la alimentación, incluyendo el plato de alimentación, constituyen la sección de agotamiento. La alimentación desciende por la sección de agotamiento hasta el fondo de la columna, donde se mantiene un nivel de líquido definido. El líquido fluye por gravedad hasta el calderín, que genera vapor y lo devuelve al fondo de la columna, comenzando así el ascenso por la columna de dicho vapor. Del calderín se extrae el producto de cola. Los vapores que llegan a la parte superior de la columna se condensan totalmente en un condensador. Parte de este condensado se devuelve al plato superior de la torre y parte se extrae como producto. Esta corriente de líquido recibe el nombre de reflujo. El líquido que desciende es el que iteraciona con el vapor ascendente. Si no se forman azeótropos, los productos de cabeza y cola pueden obtenerse con una pureza elevada si hay suficientes platos y utilizando un reflujo adecuado.
Ventajas y aplicaciones
La variedad de las columnas de rectificación y sus aplicaciones es enorme. Las mayores unidades se encuentran generalmente en la industria del petróleo, pero también existen columnas grandes y plantas de destilación muy complicadas en el fraccionamiento de disolventes, en la separación del aire líquido y en los procesos químicos en general.
Diagrama de flujo
Esquema de una destilación típica con un equipo de “flash” previo. Columna de destilación
ABSORCIÓN GAS-LÍQUIDO
Principios de operación
La absorción es una operación unitaria de transferencia de materia consiste en poner un gas en contacto con un líquido para que éste disuelva determinados componentes del gas, que queda libre de los mismos. La absorción puede ser física o química, según que el gas se disuelva en el líquido absorbente o reaccione con él dando un nuevo compuesto químico. En una sección cualquiera de la columna están en contacto un gas y un líquido que no están en equilibrio, por lo que se produce una transferencia de materia. La fuerza impulsora actuante es la diferencia entre la presión parcial en el gas del componente que se transfiere y la presión parcial que tendría el componente en un gas que estuviera en equilibrio con el líquido del punto considerado
Descripción de la instalación
Un aparato frecuentemente utilizado en absorción de gases es la torre de relleno. El dispositivo consiste en una torre equipada con una entrada de gas y un espacio de distribución en la parte inferior, una entrada de líquido y un distribuidor en la parte superior; salidas para el gas y el líquido por cabeza y cola, respectivamente; y una masa soportada de cuerpos sólidos inertes que recibe el nombre de relleno de la torre, el cual puede ser cargado al azar en la torre o bien ser colocado ordenadamente a mano. La entrada de líquido se distribuye sobre la parte superior del relleno mediante un distribuidor y, en la operación ideal, moja uniformemente la superficie del relleno. El gas que contiene el soluto asciende a través de los hendiduras del relleno en contracorriente con el flujo de líquidos, y así el líquido se enriquece de soluto a medida que desciende por la torre. El relleno proporciona una gran área de contacto entre el líquido y el gas, favoreciendo así un íntimo contacto entre las fases, y la mayoría de los rellenos de torre se construyen con materiales baratos, inertes y ligeramente ligeros, tales como la arcilla, porcelana o diferentes plásticos. A veces se utilizan anillos metálicos de pared delgada, de acero o aluminio. Por último cabe mencionar que el diámetro de una torre de absorción depende de las cantidades de gas y líquido tratadas, sus propiedades, y la relación de una corriente a otra, y que la altura de la torre, y por tanto el volumen del relleno, depende de la magnitud de las variaciones de concentración que se desean y de la velocidad de transferencia de materia por unidad de volumen de relleno.
Ventajas y aplicaciones
Uno de los ejemplos típico es la absorción de amoniaco contenido en una mezcla con aire, mediante tratamiento con agua líquida. El soluto se puede recuperar posteriormente del líquido por destilación y el líquido absorbente puede desecharse o bien ser reutilizado. En definitiva, la absorción gas-líquido se utiliza siempre que tengamos una corriente gaseosa, en la cual haya un componente que queramos eliminar, desde los procesos petroquímicos hasta la purificación de un residuo gaseoso.
Diagrama de flujo
Proceso de lavado de un gas. Absorción gas-líquido
EXTRACCIÓN LÍQUIDO-LÍQUIDO
Principios de operación
Esta técnica se utiliza para separar dos líquidos miscibles utilizando un disolvente que disuelve preferentemente a uno de ellos. En extracción es preciso recuperar el disolvente, generalmente por destilación, para su reutilización y la operación combinada es más compleja y, con frecuencia más costosa que la destilación sola sin extracción. Puesto que la mayor parte de los métodos de extracción continua usan contactos en contracorriente entre dos fases, muchos de los fundamento de la absorción de gases se pueden aplicar a la extracción líquido-líquido, cuestiones como etapas ideales, eficacias, etcétera.
Descripción de la instalación
En extracción, lo mismo que en absorción de gases, es preciso poner en buen contacto dos fases para permitir la transferencia de materia y separar después las fases. Con frecuencia las fases son difíciles de mezclar y todavía más difíciles de separar. El extracto es la capa de disolvente más el soluto extraído y el refinado es la capa de la que se ha separado el soluto: el extracto puede ser más o menos denso que el refinado, de forma que pueda salir por la parte superior del equipo y otras por el fondo. Los equipos de extracción más representativos son columnas de pulverización, torres de relleno y columnas de platos perforados. Uno de los más sencillos es la torre de pulverización, la cual opera en contacto diferencial y no por etapas, teniendo lugar la mezcla y sedimentación de forma simultánea y continua. El líquido menos denso se introduce por el fondo y se distribuye en pequeñas gotas por medio de las boquillas A. Las gotas del líquido ligero ascienden a través de la masa de líquido más pesado que desciende por la torre como una corriente continua. Las gotas se recogen en l a parte superior y forman la corriente del líquido más ligero que sale por la cima de la torre. El líquido más pesado sale por el fondo de la torre. Hay una transferencia continua de materia entre las fases, y la composición de las fases varía a medida que circula por la torre. La velocidad de transferencia es relativamente baja en comparación con absorción o destilación y una columna alta puede ser equivalente a sólo una pocas etapas ideales. Se puede aumentar la transferencia de materia en la torre, llenando la columna con cuerpos de relleno tales como anillos o monturas.
Ventajas y aplicaciones
Cuando la separación por destilación es ineficaz o muy difícil, la extracción líquido-líquido es una de las alternativas a considerar. Uno de los principales usos son las mezclas con las temperaturas de ebullición próximas, como derivados del petróleo, o sustancias que no pueden soportar la temperatura de destilación, con frecuencia se separan por extracción, que utiliza diferencias de estructura química en vez de diferencias de volatilidades. La extracción puede utilizarse para separar más de dos componentes y en algunas aplicaciones se requiere una mezcla de disolventes en vez de un solo disolvente.
Diagrama de flujo
Extracción de ácido acético en disolución acuosa. Extracción líquido-líquido
INTERCAMBIO IÓNICO
Principios de operación
El intercambio iónico se basa en la adsorción, el cual es un proceso de separación en la que ciertos componentes de una fase fluida se transfieren hacia la superficie de un sólido adsorbente. Generalmente las pequeñas partículas de adsorbente se mantienen en un lecho fijo mientras que el fluido pasa continuamente a través del lecho hasta que el sólido está prácticamente saturado y no es posible alcanzar ya la separación deseada, con lo cual el lecho se ha de regenerar La mayor parte de los adsorbentes son resinas, compuestos orgánicos de gran peso molecular que tiene la propiedad de disponer de un residuo catiónico o aniónico intercambiable, y gracias a su alta porosidad, la adsorción puede tener lugar fundamentalmente en el interior de las partículas, y aumentado así el área de contacto. La separación se produce debido a la diferente afinidad de las resinas con los cationes y aniones que se desean eliminar, y por tanto la buena elección del lecho favorecerá la separación de los iones y la eficacia dependerá del equilibrio sólido-líquido y de las velocidades de transferencia de materia.
Descripción de la instalación
Un aparato de adsorción está constituido normalmente por un recipiente cilíndrico, cerrado, que en su interior contiene la resina. Debido a los dos tipos de resinas, catiónicas y aniónicas, se acostumbra a colocar adyacentes dos columnas, cada una con un tipo de resina, para así eliminar primero los cationes y con posterioridad los aniones. Las partículas de adsorbente se colocan en un lecho soportado sobre una matiz o placa perforada. La alimentación circula a través del lecho en sentido descendente, y cuando la concentración de soluto en el fluido de salida alcanza un cierto valor, o bien para un tiempo previamente establecido se ha de parar la operación y pasar a regenerar dicho lecho. Para evitar estos inconvenientes, en el trabajo continuo, se colocan dos columnas, y así mientras una trabaja la otra efectúa la operación de regeneración. La regeneración de una resina catiónica se lleva a cabo añadiendo un ácido fuerte, aportar H+, mientras la aniónica se regenera con bases, compuestos que aporten OH-
Ventajas y aplicaciones
Este es un proceso típico para ablandar o desionizar el agua, aunque es recomendable aplicarse después de un tratamiento previo adaptado a cada calidad de agua bruta, y que consista, especialmente, en la eliminación de las materias en suspensión, materias orgánicas, cloro residual, cloraminas, etcétera.
Diagrama de flujo
Esquema de un proceso de desionización de agua. Intercambio iónico
SEPARACIÓN POR MEMBRANA
Principios de operación
En un equipo de este tipo, una membrana de material polimérico separa dos fluidos con concentraciones diferentes de una determinada sustancia. La membrana impide el flujo hidrodinámico entre los dos fluidos. Sin embargo, es permeable con respecto a la sustancia en cuestión, permitiendo su difusión al fluido con una menor concentración y haciendo posible así la extracción de parte de la sustancia no deseada de la corriente que la contenía inicialmente. Las películas poliméricas en general, pueden ser entendidas como un conjunto de regiones cristalinas y amorfas entremezcladas. Las regiones cristalinas presentan estructuras regulares que hacen muy difícil la difusión de cualquier sustancia a través de ellas y que son consideradas impermeables. Son las regiones amorfas las que pueden permitir el paso a determinadas moléculas.
Descripción de la instalación Como ya se ha dicho, las membranas están fabricadas de material polimérico. Sus espesores son del orden de micras y varían según los casos. Existe una amplia variedad de diseños de unidades de separación por membrana. En concreto, para la separación de gases, tres son los modelos más frecuentemente utilizados:
– el modelo "hollow-fiber"
– el modelo "spiral-wound"
– el modelo de plato y carcasa
Ventajas y aplicaciones
El uso de técnicas de separación por membrana de líquidos o gases resulta muy válido para separar mezclas de compuestos con propiedades físicas y químicas similares, mezclas de isómeros y mezclas que contienen sustancias térmicamente inestables. Este tipo de procesos es particularmente útil como técnica de separación cuando otras más convencionales no son económicamente recomendables para obtener unas especificaciones de producto determinadas. También suele emplearse complementando a otras técnicas más clásicas. Por ejemplo, una unidad de separación de membrana puede utilizarse para romper una mezcla azeotrópica antes de que ésta sea alimentada a una columna de destilación.
Diagrama de flujo
Esquema de un proceso en el que se utiliza un equipo de separación por membrana para romper una mezcla azeótrópica de dos componentes (comp1, comp2) antes de someterla a un proceso de destilación. Separación por membrana
ÓSMOSIS INVERSA
Principios de operación
La ósmosis inversa separa un soluto de una disolución forzando al solvente a fluir a través de una membrana mediante la aplicación de una presión superior a la presión osmótica normal. En la ósmosis inversa, las moléculas de soluto son de un tamaño similar al de las moléculas de disolvente. Al contrario que otras operaciones unitarias como la destilación, este proceso permite operar a temperatura ambiente. Además, combina simplicidad técnica con versatilidad.
Descripción de la instalación
Los materiales más frecuentemente utilizados en la fabricación de las membranas son el acetato de celulosa y las poliamidas aromáticas. Cuatro son los modelos más comunes empleados en la separación por ósmosis inversa:
– el modelo "hollow-fiber"
– el modelo "spiral-wound"
– el modelo de plato y carcasa
– el modelo tubular
Ventajas y aplicaciones
A pesar de que la ósmosis inversa se utiliza fundamentalmente en la desalinización de agua, ya sea para consumo humano o para uso industrial, también resulta frecuente su uso en procesos de producción de sustancias inestables térmica o químicamente en los que los métodos tradicionales de separación provocan pérdida de producto o deterioro de su sabor (medicinas, alimentos…). La ósmosis inversa también se emplea para fraccionar mezclas de materiales difíciles de separar por otros medios, como polímeros naturales o sintéticos.
Diagrama de flujo
Esquema de un proceso de desalinización de agua de mar. Ósmosis inversa
CENTRIFUGACIÓN
Principios de operación
El equipo gira alrededor de un eje, generando así una fuerza centrífuga que hace que las partículas de la fase más pesada se dispongan formando una capa lo más alejada posible del eje de rotación, todo lo contrario que ocurre con las partículas de la fase más ligera.
Descripción de la instalación
Podemos hablar de tres tipos fundamentales de separadores centrífugos
– centrifugador "tubular-bolw". Gira a velocidades muy altas, generando fuerzas centrífugas del orden de 13,000 veces la fuerza de la gravedad. Está construido para operar con caudales de entre 200 y 2,000 litros/hora. Al no disponer de un sistema de extracción automático, sólo puede trabajar con concentraciones pequeñas de sólidos.
– centrifugador "disk-bowl". Gira a una velocidad inferior al anterior y genera una fuerza centrífuga 7,000 veces la de la gravedad. Puede manejar caudales de hasta 20,000 litros/hora con cantidades moderadas de sólidos.
– centrifugador "solid-bowl". Su velocidad de giro provoca fuerzas centrífugas de 3,000 veces la de la gravedad. Es capaz de trabajar con corrientes que contienen gran cantidad de sólidos, separando hasta 50 toneladas/hora de esas sustancias.
Ventajas y aplicaciones
Esta clase de separadores están diseñados para operar con corrientes líquido-sólido y líquido-líquido-sólido. Los sistemas gas-sólido se separan por medio de otro tipo bien diferenciado de equipos que son los ciclones.
Diagrama de flujo
Esquema de un proceso de producción de polipropileno en el que se utilizan dos equipos de centrifugación para separar el polvo de polipropileno del disolvente. Centrifugación
SEPARACIÓN ELECTROSTÁTICA
Principios de operación
La separación electrostática es un método de separación basado en la diferente atracción o repulsión de partículas cargadas bajo la influencia de un campo eléctrico. La aplicación de una carga electrostática a las partículas es un paso necesario antes de que su separación pueda tener lugar. Tres son las técnicas más utilizadas para dotar a las partículas de dicha carga:
– electrificación por contacto entre materiales con propiedades muy diferentes.
– inducción conductiva, la cual tiene lugar al poner en contacto una partícula inicialmente no cargada con una superficie que sí que lo está.
– bombardeo de iones de gases atmosféricos. Este es el método más poderoso de electrificación.
Descripción de la instalación
Los separadores electrostáticos pueden dividirse en tres grandes grupos según que sistema de electrificación de partículas se utilice. Dentro de cada uno de estos grupos, existen varias clases. La más extendida industrialmente es la de los "conductive roll separators", que utilizan el bombardeo iónico como técnica de electrificación de las partículas.
Ventajas y aplicaciones
Las aplicaciones de este tipo de separadores son diversas: – separación de minerales en cadenas de purificación de extracciones mineras.
– extracción de partículas no metálicas contenidas en polvos metálicos.
– separación de piedra y arena de verduras y hortalizas en una primera fase de su procesado.
– extracción de partículas en el tratamiento de aguas. Mediante este tipo de equipos, resulta muy difícil separar partículas con un tamaño inferior a 0.074 mm, y prácticamente imposible si su tamaño es inferior a 0.044mm.
La inversión a realizar cuando se quiere adquirir uno de estos equipos es grande, aunque los costes de operación no son demasiado elevados.
Diagrama de flujo
Esquema de un proceso típico de separación de partículas. Separación electrostática
BIBLIOGRAFÍA
Perry R.H., Green D. / "Perry’s Chemical Engineers Handbook" / McGraw-Hill / 1988.
McCabe W.L., Smith J.C. / "Unit Operations of Chemical Engineering" / McGraw-Hill / 1993.
Coulson J.M., Richardson J.F., Sinnot R.K. / "Chemical Engineering" / Pergamon Press / Vol. 6 / 1993.
Bioseparación, cromatografía de gel
Hacía tiempo que no posteaba en la categoría de Ingeniería Química, supongo que al no estar metido en este mundo en su día a día como hace unos años, ha hecho que este apartado un poco de esta especialización científica. Pero esto no me ha impedido revisar mis viejos apuntes universitarios para rescatar información que quizás pueda interesar a alguien, y que iré publicando poco a poco en este blog.
El trabajo que os adjunto hoy lleva por nombre, Bioseparación, cromatografía de gel. Es un proyecto que hice hace más de 10 años, pero a diferencia del universo informático, las cosas en la Ingeniería Química no corren tan deprisa, por lo que el concepto que se explica en este trabajo sigue siendo vigente.
El método de cromatografía de gel explota las diferentes propiedades físicas debidas a la diferencia de tamaño molecular, consiguiendo de esta forma la separación entre elementos. Este método es el de mayor aceptación en la separación de miles de proteínas, ácidos nucleicos, enzimas, polisacáridos y otras biomoléculas.
Obtención del cloruro de vinilo
La destacada importancia del cloruro de vinilo como monómero universal en la obtención del hom-, co- y termopolímeros se refleja en el impetuoso crecimiento de su producción industrial. El cloruro de vinilo es la base para la fabricación del cloruro de polivinilo, más conocido coloquialmente como PVC, material que usado en forma plastificada es utilizado para gran cantidad de aplicaciones. ¿Quién no ha oído hablar nunca del PVC?
Hoy os adjunto un trabajo datado del 1993. Pese a los años y avances tecnológicos, la base para la obtención del cloruro de vinilo sigue siendo vigente, aunque las cifras que se mencionan en el trabajo deberían actualizarse.
Plásticos
Los plásticos podrían definirse como un gran número de productos de origen orgánico y de alto peso molecular, que son sólidos en su estado definitivo, pero que en alguna etapa del proceso de su fabricación son suficientemente fluidos para ser moldeados por calor y presión.
En este trabajo que realice el año 1995 os muestro la constitución, estructura y tipos, transfromación, tratamiento y aplicaciones de los plásticos.
Hidrogenación catalítica selectiva de CFC’s
Presentación realizada en el año 2001, cuando estudiaba el primer curso del Doctorado de Ingeniería Química, sobre la Hidrogenación catalítica selectiva de CFC’s, y su transformación en productos útiles. Los CFC’s están considerados desde hace décadas, como los mayores causantes de la destrucción progresiva de la capa de ozono.
Según la Wikipedia:
Los clorofluorocarbonos o clorofluorocarbonados (denominados también ClFC) es cada uno de los derivados de los hidrocarburos saturados obtenidos mediante la sustitución de átomos de hidrógeno por átomos de flúor y/o cloro principalmente.
Los CFC son una familia de gases que se emplean en múltiples aplicaciones, siendo las principales la industria de la refrigeración y de propelentes de aerosoles. Están también presentes en aislantes térmicos. Los CFC poseen una capacidad de supervivencia en la atmósfera, de 50 a 100 años. Con el correr de los años alcanzan la estratosfera donde son disociados por la radiación ultravioleta, liberando el cloro de su composición y dando comienzo al proceso de destrucción del ozono.
Hoy se ha demostrado que la aparición del agujero de ozono, a comienzos de la primavera austral, sobre la Antártida está relacionado con la fotoquímica de los Clorofluorocarbonos(CFCs), componentes químicos presentes en diversos productos comerciales como el freón, aerosoles, pinturas, etc.
Proceso de obtención del Permanganato potásico
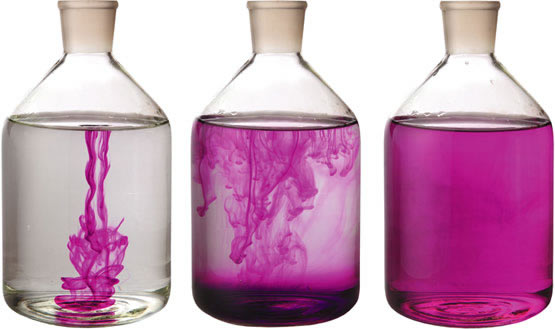
Rebuscando en mis apuntes de estudiante he encontrado un trabajo que realice hace casi 20 años, el Proceso de obtención del Permanganato potásico. Desconozco si totalmente sigue siendo de valor dicho trabajo, pero aunque seguramente se han mejorado los procesos productivos, la esencia de la obtención estoy casi seguro que es la misma.
El procedimiento para la obtención del permanganato potásico se divide en dos partes:
A) Preparación del manganato
B) Oxidación del manganato
Y en el siguiente documento os la explico, o mejor dicho os lo explicaba en el año 1993.
Qué tipo de equipo es el diagrama de Extracción Líquido-Líquido?